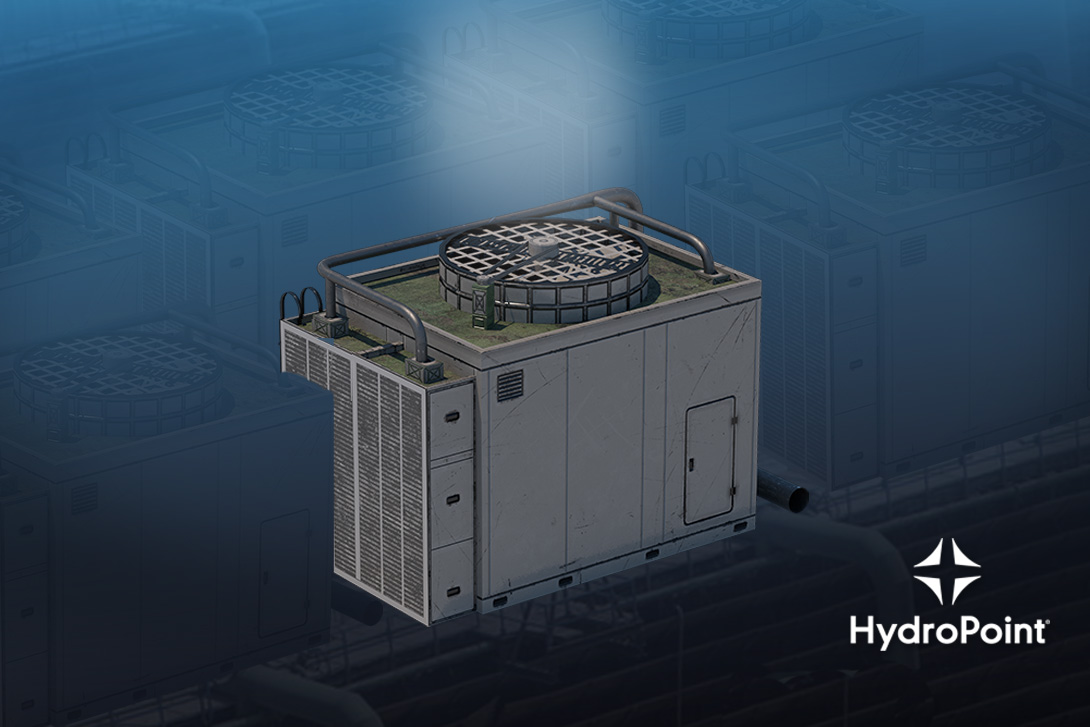
Everyone knows that water cooling towers consume huge volumes of water. In some cases, as much as 50 percent of a building’s domestic water use. But by following a few best practices, facilities can save significant amounts of water. Here are 8 ways to improve water cooling tower efficiency and lower water consumption.
Maximize cycles of concentration
The more times you can recycle water before it needs to be dumped, the less water you will need to use. Many systems operate at two or four cycles of concentration, depending on the quality of the make-up water and the water treatment regimen. Treatment systems to monitor and minimize chemical use reduce the potential for corrosion, scaling, and biological growth. This allows a tower to operate safely at higher concentration ratios. Increasing from three to six cycles would reduce make-up water by 20 percent and blowdown by 50 percent. Consider working with a water treatment vendor or local water agency to investigate treatment options.
Reduce blowdown through monitoring and set points.
To minimize scaling and biological growth, many operators increase the frequency of blowdown water, which increases water waste. While this method seems proactive, it may also increase corrosion by lowering the pH. The only true solution is careful pH monitoring, and establishing and adhering to set points.
Install a conductivity controller.As it relates to cooling, conductivity is the ability to conduct electricity with relation to the amount of dissolved minerals in the water. By measuring conductivity and only discharging water only when the conductivity set point is exceeded, you will use water more efficiently.
Install flow monitors on make-up and blowdown lines.
Many water agencies charge companies for disposing of waste water from water cooling towers. They bill based on the amount of water that goes into the make-up line, on the presumption that all of the water that goes into a facility is ultimately disappearing down the drain. To avoid incurring waste water charges for the significant amount of water that evaporates in the cooling process, we recommend installing a flow monitor at each end. The flow monitors document how much water came in to the tower and how much went out, so you only pay waste charges for water output.
Monitor water levels.Switch from ballcock-style fill valves that are unreliable and prone to leakage to more reliable fill valves. You can also waste water when the fill level is set too high. In that case, strong airflow in the sump causes choppiness on the water surface that results in overflow. The water level should be regularly checked to ensure it is safely below the overflow outlet to reduce excessive water waste.
Maintain air handler coils.
As coils become dirty, the load on the chilled water system increases as it tries to maintain its set point temperatures. This easily avoidable maintenance issue increases electricity usage, taxes the evaporative cooling process, and wastes additional water.
Choose a water treatment vendor committed to conservation.Ensure your vendor understands that water efficiency is a shared priority. Running things more efficiently means you will need to buy fewer chemicals from them. Select a vendor based on its cost to treat make-up water and maintain a cooling tower with the highest possible cycles of concentration.
Subscribe to a flow monitoring service.
Services like HydroPoint® WaterCompass® provide the visibility and analytics needed to detect leaks and monitor water usage. It constantly tracks cooling tower performance and increases efficiency by automating a largely manual process. Easily track make-up, make-up to blowdown ratio, cycles of concentration, and number of alert days, as well as compare results across several water cooling towers